One of the leading lamp manufacturing companies wiped out opacity in their manufacturing process by implementing LUMIS application. The company had challenges in production surveillance and in achieving data transparency in the manufacturing processes. The deployment of LUMIS application strips out obscurity in the manufacturing process and helps the company in achieving manufacturing excellence.
About the Client
The company is a joint venture between a leading Japanese lamp manufacturing company and eminent auto parts manufacturing company in India. The company is renowned in automotive lamps market. The company wanted to overhaul their production surveillance by harnessing groundbreaking technologies in the IT industry.
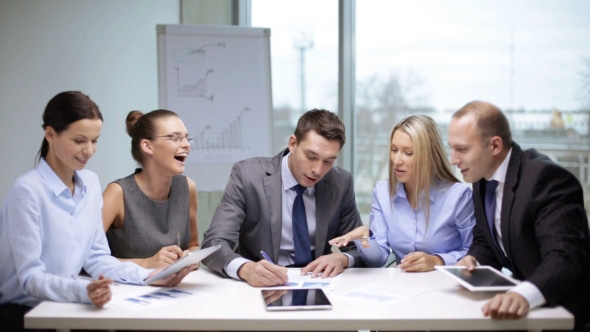

Business Challenge
Lamp manufacturing involves numerous processes and subprocesses, and every process has standard output and rejection rates. The production department in the company encountered disproportionate production outputs i.e, the quantum of the output and wastage did not commensurate with the quantum of input of raw materials. Besides, the company could not ascertain the concrete reason behind this disproportion which had been greatly detrimental in company’s way of achieving substantial profits.
Elintsys’ Solution
Elintsys underwent the thorough study of all the processes, sub-processes involved in the manufacturing processes and learned that capturing real-time data at the end of every process and subprocess is indispensable to get rid of obscurity in production surveillance. Elintsys developed an integrated application to capture real-time data along with the reason for rejection at the end of every process and subprocess; furthermore, Elintsys’ application regulated the material supply from stores department, the application ensured only the required quantity of materials based on the production budget shall be supplied, i.e., the supplied quantity shall not be more than or lower than the required quantity for production on a day.
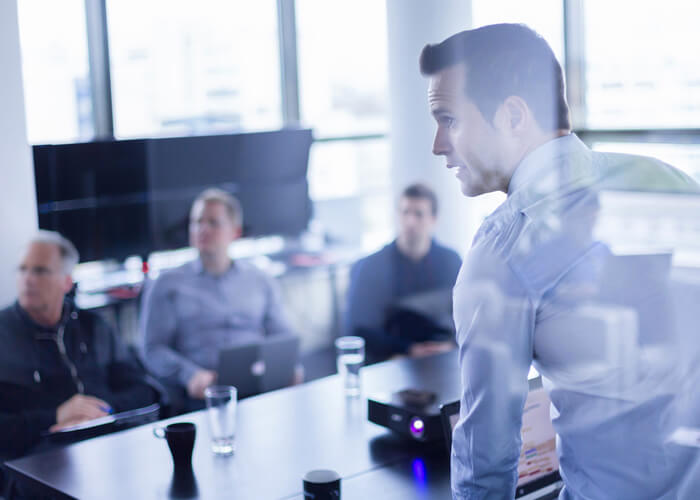

Results
The application has been instrumental in achieving manufacturing excellence by bringing out the following benefits.
- Ensured real-time capturing of data at the end of every process and subprocess along with the reason for rejection. The application shed light on real-time manufacturing data on the Shop Floor.
- The conundrum of disproportionate production results has been eliminated with the assistance of application.
- The application obviated material shortfall and material redundancy that facilitated the optimized supply of raw materials which is necessary to trim production overheads.
- With better data transparency, the efficaciousness of production planning and its subsequent better production management has been dramatically enhanced.